Final results of the MAREWIND project!
07 January 2025
Over the last four years, the MAREWIND partners from leading industry, technological and research organisations have delved into the exploration of new materials, gathered experimental data, and created predictive models. These efforts aim to enhance the durability, minimise maintenance requirements, and reduce environmental impacts in the offshore wind energy sector.
The MAREWIND project has developed specific functional coatings, advanced concrete formulations and novel composites as well as monitoring technologies that not only push the boundaries of functionality but also prioritise sustainability. The advancements have been done in various areas, each contributing to the overall progress of offshore wind materials.
The anti-corrosion coating, applied to the W2Power Floating Structure located in the Canary Islands (Atlantic Ocean) has shown no signs of corrosion, proving the effectiveness of the solution for future applications. Additionally, the anti-corrosion coating solutions have also shown significant advancements when focusing on repairing critical turbine components, treating vulnerable areas, and targeting the most at-risk sections.. One of the main advantages of the mentioned protective coating, implies direct application by spraying, but also, the compatibility with paints required by marine visibility regulations.
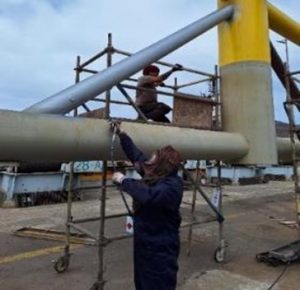
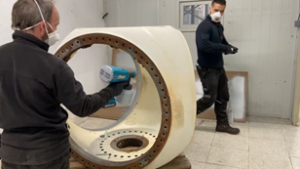
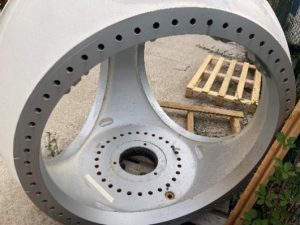
Turning to the antifouling coating, the assessments of samples submerged in Sines (Portugal), as part of the Gravity-Based Structure (GBS), have revealed the unique attributes of the low-thickness product. These tests demonstrate its superior adhesion when compared to commercial alternatives, showcasing its potential for enhanced performance. In parallel, other antifouling coatings are undergoing tests in the Mediterranean waters at “Observatoire Océanologique de Banyuls-sur-Mer” to further expand our research and results.
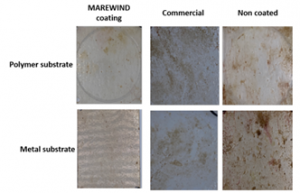
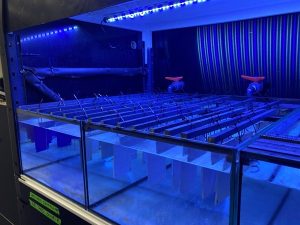
The results of the test carried out, showed clear antifouling effect for the MAREWIND coating after 7 months of exposure, and even better performance, compared to commercial benchmark. The tests included not only visual inspection, but also biofouling monitoring by mass and surface concentration of chlorophyll a.
Additionally, treated coupons embedded in frames with anticorrosion and antifouling coatings have been installed in offshore wind farm in Teesside (North Sea). These frames are positioned across three different exposure zones: the subsea zone, atmospheric zone, and intermediate splash conditions. Over the course of the project, various inspections have been run to assess the performance and durability of these innovative coatings.
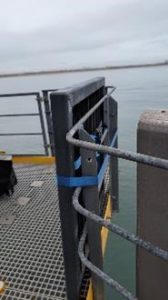
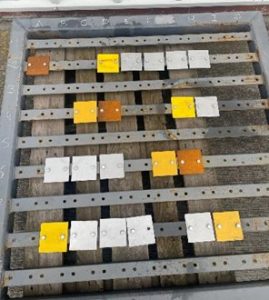
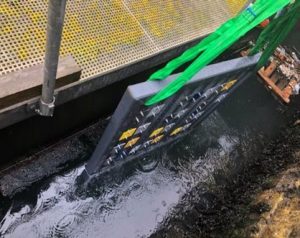
Test conducted across atmospheric, splash zone, and subsea conditions
The first analysis carried out showed no corrosion on the MAREWIND samples for both atmospheric and splash zones after 6 months of exposure. Next, the newly developed concrete formulations offer enhanced durability and improved sustainability for offshore environments. On the one hand, the Ultra High-Performance Concrete (UHPC) is expected to outperform current commercial options, offering a durable, preventive solution during production. It also shows strong potential for maintenance and repair applications, where its durability and resilience can extend the lifespan of structures in demanding environments. Currently, real exposure tests are ongoing in Gijón Harbour.
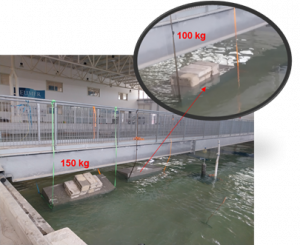
On the other hand, the project has developed sustainable and cost-efficient concretes based on Alkali-Activated Materials (AAMs) that demonstrate durability, excellent flow capacity for molding, and strong resistance to freeze-thaw cycles. Suitable prototypes were manufactured with both concrete technologies, validated at real exposure in subsea conditions (AAM in GBS in Portugal).
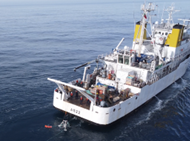
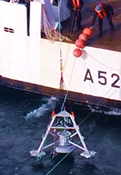
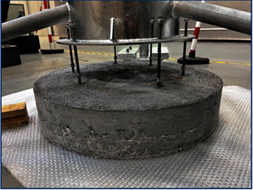
GBS in Sines (Portugal). Analysis after 6 months exposure in the GBS submerged in Sines.
Additionally, the project has successfully produced a 13-meter blade using an innovative composite technology from recyclable resin, incorporating a circular sustainable design, and including validation by mechanical tests in CTL (Galway). By combining these advanced materials and Structure Health Monitoring technology, the project enhances resource management and structural integrity in offshore infrastructure.
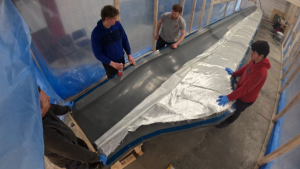
Key improvements include the integration of Fiber Reinforced Polymer (FRP) bars in novel concrete formulations within innovative concrete formulations and the embedding of Fiber Optic Sensors across blades, gravity-based structures (GBS), and concrete structures. Additionally, external blade inspections conducted with advanced drones provide a comprehensive view of structural condition.
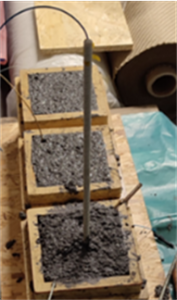
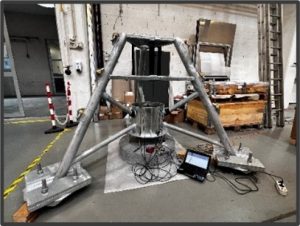
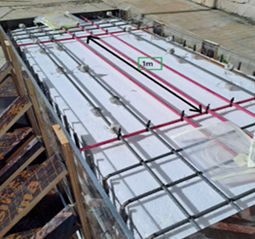
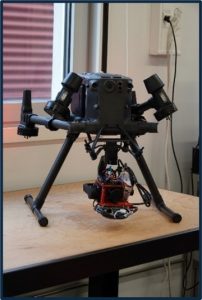