During the first 18 months of the project, the main effort has been focused on the design of high, ultrahigh performance concrete and Alkali Activated concretes that fulfil offshore infrastructures requirements. In addition, EDF has performed tests to evaluate the durability of concrete under exposure to the real environment through aging tests. It also provided support on floating offshore concrete structures, including contribution on modeling of the structures that will be used to design the prototypes to be tested.
High and ultra-high Concrete material
The reference material (Class C60 concrete) was defined from a previous experience on offshore concrete design. The work was focused on new advanced concrete materials design. After preliminary laboratory trials for the optimal raw material selection, the proper combinations were selected for high and ultra-high concrete mixtures design.
To fulfil the high performance concrete requirement, 9 dosages were casted and tested. Thedesign and optimization of the ultra-high concrete was more challenging compared to HPC, due to the occluded air that remained in the samples in the casting process.
According to the standard recommendations, HPC has low potential for cracking under restrained conditions; UHPC with PVA fibres has moderate-low potential, UHPC without SAP (super absorbent polymer) additive has moderate-high potential, UHPC with SAP additive and conventional concrete have high potential for cracking under restrained conditions. Thanks to the higher content of SCM in UHPC samples, the heat of hydration of these mixes in lower than for HPC. Therefore, showing very promising results for the advanced concrete materials developed within this task.

Alkali Activated concrete
CETMA has focused on the development of alkaline activated conglomerates (AAC), considering only alkaline activators, glass powders and blast furnace slag were used as binder.
Since alkaline activated materials have a very viscous behaviour and generally have very fast setting times, they are hard materials to mix. To avoid excessive consumption of materials and safeguard equipment, the experimental program was divided into three different phases:
-
First phase: the behaviour in the fresh and hardened state of the binder composed of glass powders, blast furnace slags and activators such as water, sodium silicate and sodium hydroxide were characterized.
-
Second phase: previously optimized binder was mixed with four different types of sand for the realization and characterization of alkali activated mortars.
-
Third phase: based on previously characterized binder and mortars, AAC mix design containing three different types of aggregates was carried out.
To increase AAC mix sustainability, optimized binder-recycled aggregates compatibility was studied. Furthermore, very fine natural magnetite was used to increase the density and try to reduce the cracking phenomena caused by the heat of hydration. After choosing the best performing mix design to achieve project specifications in terms of compressive strength, consistency and workability, a final proportion optimization and repeatability study was performed.
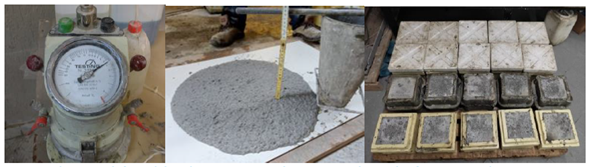
MAREWIND concretes durability characterization
For durability characterization of new concrete materials developed in MAREWIND project, several tests were carried out. Test results show that advanced concretes, as it was expected, are able to achieve better durability performance than standard C60 offshore concrete . Both advanced concretes showed in general, the same durability results, only in corrosion rate and probability UHPC presents a slight risk. Despite these slight differences, UHPC will be used on the prototype manufacturing due to its SCC behavior, that allows slender structures more suitable to keep floating structure’s buoyancy.
AAC presented similar behavior as C60 concrete in chloride penetration resistance, it showed better performance at early-ages to water penetration, whereas it seemed to be likely to develop corrosion risk during it service life. A deeper analysis will be carried out when all the ages results will be available, to check if this tendency keeps in time or not.
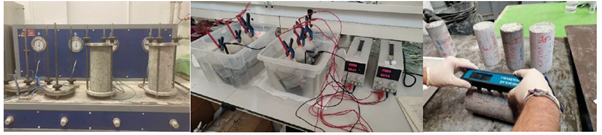
Durability of concrete samples exposed to a real environment
EDF performed the reference characterization of the durability properties of an ordinary offshore concrete mixture in their offshore facilities.
Chloride ingress in permanent immersion and tidal zone exposure is characterized in ϕ16×32 cm cylindrical specimens. Each sample has been divided into 3 sub-specimens of ϕ16×10 cm. The obtained sub-specimens have been subjected to chloride ingress. A first group was immersed completely in seawater, whereas, a second group was subjected to wetting/drying cycles with 6 hours period using a hydraulic pump.
As result, a comprehensive database of chloride content distribution was set up. Some basic processing including the determination of the chloride apparent diffusivity and the prediction of chlorides content evolution over time were performed.
Reinforced composites production and testing
The project plan outlines three strategies for new composite formulation:
- the use of nano-SiO2
- the use of Vitrimers/TPR recyclable resins
- the use of RCF
EIRE defined a preliminary material test matrix that is being used to test the initial epoxy-SiO2 resin formulations, developed by TWI, reinforced with glass fibre and a final material test matrix to generate a material datasheet for the chosen resin modified with nano-SiO2 and also the recyclable composites laminates produced by CETMA.
The use of nano-SiO2
Regarding the use of nano-SiO2 particles, TWI characterized and functionalized pyrogenic silica and Stöber silica powders. Next, TWI carried out a study on the viscosity versus loading behaviour of different silica powders in model resin in order to establish a pathway for silica incorporation procedure.
Upon the results of rheology study, ten modified samples were prepared for EIRE, five modified powder epoxy and five modified liquid epoxy resin samples with different loading ratios. For each of those samples, 1,3-dioxolane, a solvent selected based on Hansen Solubility Parameter (energetic) considerations, was used to reduce the inherent viscosity and facilitate mixing.
EIRE Manufactured preliminary test panels using the five initial powder epoxy-SiO2 and five initial epoxy-SiO2 infusion resin samples, prepared by TWI, reinforced with UD glass fibre. On the one hand, all 5 powder epoxy – SiO2 sample panels contained an unsatisfactory surface finish. It appears that the nano-SiO2 particles are incompatible with the powder epoxy process resulting in panels that contained substantial visual defects such as, dry fibres and lumps of dry nano-SiO2 particles scattered across the panels. This was most likely the effect of uncontrolled silica particles dispersion. Those panels were deemed unfit for testing and thus, powder epoxy-SiO2 developments were not selected as preferred strategy.
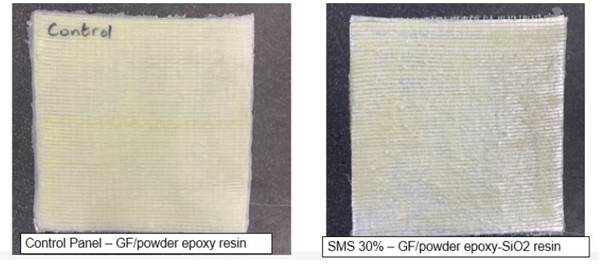
On the other hand, such dispersion problems were not associated with epoxy resin modification with 3 of the 5 epoxy-SiO2 infusion resin samples successfully infused, while the other 2 samples had a viscosity that was too high for the infusion process. EIRE carried out the preliminary material test matrix and the best performing epoxy-SiO2 infusion resin sample was chosen for the final material test matrix.
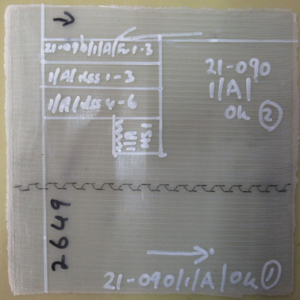
The use of Vitrimers/TPR recyclable resins
One of the project objectives states that MAREWIND will provide the design of new composites with intrinsic ability to be reprocessed and recycled, and that can also be easily processed using the same technologies used for thermosetting resin. The goal is to get a recyclable content in the composite above 40% of total. In respect to new recyclable resins, CETMA has carried out a commercial scouting to select the most suitable resin system for the wind industry in terms of physical and mechanical properties (durability and service temperature among others). Also, the composite matrix should be able to contemporary ensure recyclability requirements and suitable parameters for the intended infusion process.
Polymeric material developers’ attention is more and more focused on new types of recyclable polymer material: thermoplastics reactive resins (TPR) and vitrimers.
Based on results of preliminary material selection, it was found that industrial production of vitrimers is still under development, and among the scarce materials available to date, no commercial products were found with suitable properties for the infusion process defined, mainly regarding viscosity.
A new TPR (thermoplastic reactive resin) system Elium 188 XO, developend by Arkema has been successfully tested.
Apart from the main strategies studied, recyclable thermosets (RT) – epoxies in particular – were then investigated as an additional alternative related to recycling. The use of the cleavable amine hardener Recyclamine R101 (formerly developed and patented by Connora Technologies, USA and acquired in 2019 by Aditya Birla Chemicals, India) allows the recyclability of the matrix recovering both the clean fibers and a de-crosslinked epoxy (i.e. thermoplastic). Different epoxy resins have been preliminarily evaluated, then focusing the work on the standard system Gurit Prime 27 provided by EIRE with Recyclamine R101 hardener.
Thermal and rheological characterization of the above resins (TPR Elium 188XO and cleavable epoxy resin) were performed to analyse the reactivity of the systems, to set up the infusion parameters and also provide preliminary input data for the numerical model of such process.
The use of RCF
CETMA has set up the infusion process and manufactured composite laminates based on RCF and UD GF as reinforcements and TPR Elium and Recyclable Epoxy resin. Process optimization was performed in order to maximize the mechanical and physical properties and comparing them with traditional composite laminates based on GF and epoxy resin.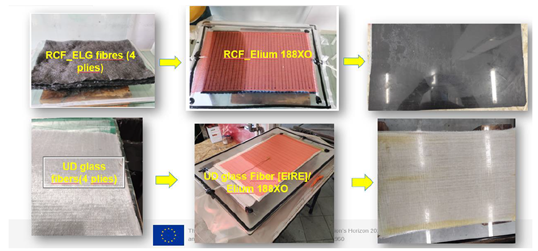
CETMA has defined the numerical model for the simulation of the resin infusion process in terms of the set-up, numerical parameters and the boundary conditions. The physical process is modelled by the Navier Stokes equations which in this case describes the mass, momentum and energy conservation of the resin flowing into a porous medium. To solve these equations the numerical method called FVM (Finite Volume Method) is used so far for the process optimization and will be used to optimize the infusion process on the full-scale demonstrator.
To solve these equations the numerical method called FVM (Finite Volume Method) is used. The model has shown great accuracy in simulating the resin flow in the infusion tests performed on small coupons and will be used to. to optimize the infusion process on the full-scale demonstrator. With regards to the thermo-mechanical recycling of TPR Elium 188XO with glass fiber laminates some preliminary tests have been done in order to evaluate the technical feasibility of these materials to be recycled and to be compression moulded, manufacturing two recycled flat panels.
CETMA has also developed a multi-scale numerical model to predict the macromechanical properties of the recycled materials based on RCF and Epoxy resin. Starting from the material properties of the composite constituents (fibres and matrix) and the microstructure characteristics (fibres volume fraction, fibres shape and orientation), a Representative Volume Element (RVE) of the composite material has been generated. A virtual characterization of RVE has been carried out to investigate the stiffness considering different loading conditions and the numerical results have been compared with the experimental ones. From the comparison was observed that the numerical results are in good agreement with the tensile modulus derived by experimental tests.
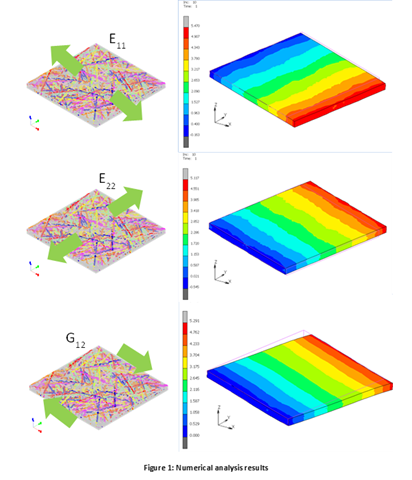
Full-field measuring techniques of wind blade working conditions
INEGI is developing a non-destructive testing system (NDT) which is intended as a first version of the final blade testing system to be developed in the coming months. The main results achieved include the definition and execution of NDT laboratory setups using DIC and IR solutions, the selection of the necessary equipment, as well as the development and successful use of the proposed trigger solutions.
Concerning the digital image correlation analyzes, two first approaches have already been carried out, namely the establishment of a system for evaluating displacements using static cameras with static blades, and them using static cameras with a rotating blade. For the defect detention system using thermography, several approaches were evaluated, and the most successful was found to be the use of an algorithm that does image comparison between thermographic images, one with a defect-free blade, used as a reference and one as the test subject.
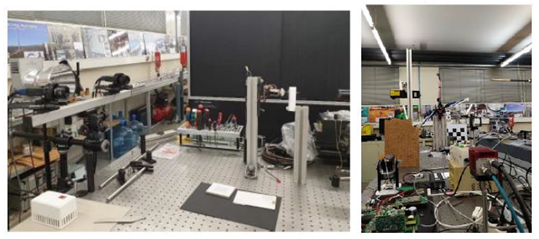
INEGI will continue with the presented plan and carry on with the remaining activities, especially with regard to the development using the structure from motion approach to carry out DIC analyzes with floating cameras, as well as with the establishment of the limits and strengths of the different thermographic approaches.
Implementation and assessment of FBGs/DFOs technologies
INEGI found that the materialization of several SHM laboratorial setups using both FBG and DFO technologies was successful, and validated the assumptions and decisions that were made, thus being ready to be implemented in the real-life scenario SHM.
Likewise, CETMA has shown the feasibility of FO distributed sensors to be applied as monitoring system in reinforced concrete structures. In particular, the developed SMART rebars (i.e., rebars with embedded FO sensors) show the following essentials points:
-
-
-
An SHM system based on SMART rebars with distributed FO sensors can provide thousands of sensing points that permits mapping of strain distributions the reinforcement of the structure.
-
The FO sensors provide the same results of traditional strain sensors in terms of reliability, with many advantages among which multiparameter measurements with the same sensor, no need of recalibration, easier wiring, high resistance in hard environment.
-
The developed embedding near surface technique of the FO sensors in the rebars is easy to realize and reliable; validation results on tensile strength test showed good behaviour.
-
The developed decoupling system permits to create segments of FO sensors not subjected to mechanical stresses.
-
The lab-trials related to the embedding process of SMART rebars demonstrated that the developed technique for the protection of the sensor in the inlet/outlet points of the FO cables both from the rebar and the concrete works properly; a 100% rate survival was achieved for all the typologies of concretes.
-
The lab trials related to mechanical tests on concrete elements with SMART rebars inside demonstrated the capability of the developed SHM system to properly detect different typologies of mechanical stresses (i.e., flexural, compression).
-
-
The activities developed will be used and furtherly implemented for SHM system for blade monitoring and concrete structures monitoring.
Modelling of GBS structure and influence of tested materials
INEGI finds as main results the definition of the design of the GBS and the study of the environmental conditions of the test site, as well as the numerical study of the structural forces on the GBS coming from the sea states and the transport and handling processes.
They also identified as the main next step to carry the planning and definition of the open sea test to be executed within the context of this project. Additionally, INEGI will continue to perform FEM simulation to study the structural integrity of the structure.
Development and validation of FEA model of composite structure for blades
The results from the MAREWIND Excel tool for the calculation of the transverse elastic and shear modulus show a better agreement with the available data using the Halpin-Tsai equations instead of the constant stress model. The MAREWIND tool has been validated for both the micro-mechanical and macro-mechanical part. Concerning the micro mechanical validation, good agreement with the reference results has been obtained. The Halpin-Tsai results are in excellent agreement with a negligible deviation.
The stress and strain calculated show excellent agreement with the reference results. Failure Analysis was performed with a unidirectional load in order to validate Tsai-Hill Failure Theory of Excel Tool and also in this case, the obtained results show an excellent agreement with the reference ones.
Likewise, the FE model tool has been validated for both the micro-mechanical and macro-mechanical part. For the macro-mechanical model, the deviations are smaller than 1% and therefore the experimental results of the literature and the numerical ones are in excellent agreement. Thus, both the micro- and macro-mechanical FE models can be considered validated.
The objective will be to use the high-resolution FE model of composite and tool to compare their results against the experimental data that will be made available by partners performing tests on the materials selected for the next phases of the project. The obtained results will be the basis for conducting the activities foreseen referred to the simulation of the blade prototype (or part of it) predict the fatigue life of the wind turbines.
A fouling-preventing coating for different materials of offshore submerged structures has been developed and characterised at laboratory scale. In the first steps, two different base coatings were developed: low curing temperature and higher curing temperature.
The complete system, in both cases, implied a two-layer treatment, with a second thin layer focused in reducing the contact of the biological matter to the surface of the different materials. In the last months, based on a room temperature curing strategy, TECNAN and Lurederra developed a one layer system with oleo and hydrophobic final properties as the two other systems. All of these base matrixes and the one-layer system matrix, have similar colour, density, viscosity and stability overtime.
In addition, samples of materials with different chemical nature were selected in order to apply and validate the coating formulations. In particular, these materials are metal, painted metal and various polymers.
Applications of the antifouling coatings
The application selected was the spray gun because of its versatility for the target substrates. TECNAN has been working in the adjustment of the parameters such as the atomisation pressure, liquid flow and the fan width among others.
In the particular case of the hydrophobic properties, considering that the contact angle 90º is a good result reference, the values obtained of the different substrates tested in all the treatments developed, are quite inspiring.

In the case of the repellence of oil, very good results have been obtained too, not only in metal but also in polymeric substrates which have low reactivity and some initial repellence that imply a bigger challenge to generate a suitable and functional coating layer on it.
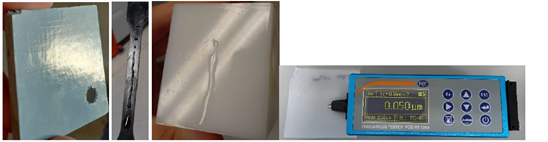
As a consequence, we could highlight the good results with the latest developed formulation based on one layer and low curing temperature, in relation with the adherence and compatibility with the substrates and the final repellence properties. The future work on the technologies validation and manufacturing, will be following this formulation strategy.
Tests in real environments
Enerocean in close cooperation with Lurederra and Tecnan, also defined and prepared the samples for the regulations ASTM D3623 and ASTM D5479, with the selected formulation ©. The materials selected for these tests were Nylon as the polymeric substrate and stainless steel as the metallic substrate. Enerocean was in charge of getting the samples and Lurederra of coating them with the protocols from Tecnan.
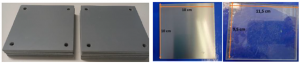
Evaluation of the coatings
EDF has carried out studies on the evaluation of the coatings. Currently, antifouling coatings are subjected to a series of conditions in order to be suitable for real applications and also, the performance must be determined by three properties:
- Ability to limit biofouling
- Low fouling adhesion and resistance of the coating to mechanical
- Chemical damages
Products belonging to the range of Chugoku Marine Paints have been selected in order to carry out comparative testing with the new solutions in development. These products consist of two different layers: ECOMAX Bi (base coat) and BIOCLEAN ECO (top coat), and it is based on non-biocidal technology. Lurederra and Tecnan have applied it and tested it on some substrates showing that the final thickness of the mentioned commercial product layers is quite significant meaning that the weight of the structures can increase in a considerable way, its appearance can change and the application can be extremely difficult.

Based on the commercially available systems, the selection of the wind turbine blade coating for trials was undertaken. In order to achieve the desired repellence (superhydrophobicity) and erosion resistance, TWI has incorporated functional additives into the selected coating matrix. All selected additives were based on materials which have previously been demonstrated to be platforms for superhydrophobic surfaces.
These additives are inorganic metal oxides that are capable of surface functionalisation to enable their native hydrophilic surfaces to be transformed into exhibiting hydrophobic behaviour. The key additives explored are:
Stöber derived TWI silica
Metal oxides (TECNAN’s silica manufactured using pyrogenic methods and commercially available pyrogenic silica Aerosil 200)
The mentioned functionalized silicas were incorporated into PU model matrix system in a various combinations and various loading levels. TWI have undertaken wettability, abrasion, adhesion and chemical resistance tests, whereas EIRE took care of rain erosion examination. INL have been given coated samples to perform long-term weatherability study.
All developed coatings improved the repellent characteristics of commercial model matrix system. Satisfactory results were also obtained from adhesion, abrasion and chemical durability tests. Nevertheless, the erosion resistance of those coatings was still not reaching target values and therefore, second generation coatings were developed.
Next steps
Further minor coating modifications will be done – addition of second functionalization might be necessary in order to bind silica particles with model matrix system via covalent bonding and thus, to increase the resistance towards rain erosion. The result from the rain erosion study suggested that developed coatings were too hard and this is not beneficial in terms of providing the resistance towards flowing water. Therefore, silica microparticles won’t be functionalized at all, to prevent and increased hardness caused from bonding together or to the matrix.
During the first 18 months of the project, the MAREWIND Consortium has been working on the development of an anticorrosion coating for key metallic elements. The coating consists of three layers with different chemical compositions and, therefore, different corrosion protections. Moreover, the multilayer system has been developed layer by layer:
-
Layer 1 has a metallic composition providing the substrate with a good cathodic protection. Considering the low curing temperature and stability overtime, two main matrix formulations were investigated, as well as various metallic components and loads.
-
Layer 2 incorporates a self-healing system based on core-shell micro/nanofibers. Nanofibers were produced and optimized regarding viscosity of each material and prepared by electrospinning technique. Then, they were completely characterised in terms of textural, morphological and chemical properties, revealing an increase in corrosion protection close to 40 times.
-
Layer 3 was designed as an Organic Inorganic Hybrid (OIH) sol-gel matrix with reinforcements of fibres and ceramic nanoparticles. The formulation has been adapted and optimised to provide the coating with additional properties such as increased mechanical strength and hydrophobicity to protect even more the target metallic offshore structures.

Different systems were proposed regarding matrices and curing procedures at low, medium and high temperature. Also, an exhaustive work regarding coating application methods as well as the characterisation of coated samples has been performed. With these results, finally the system of anticorrosion coating has been achieved in low temperature strategy.
Coating application systems
Two strategies were designed for this purpose:
- Application via spray gun:
A suitable procedure depends on the adjustment of the spray gun parameters to obtain uniform and smooth coatings. TECNAN was able to generate a reference protocol for each layer defining main parameters involved in the application process such as atomization pulverization, flow rate.
- Application via dip coating:
Dip coating is more appropriate for applying the coatings on a large number of small metallic elements. A small-scale device has been designed for a preliminary adjustment of the coating application.
The results show that spraying is the main alternative, since it provides a good surface finish, being applicable for different morphologies and sizes, while immersion is more focused on small elements with very complex geometries. Also a successful application of whole protections systems has been carried out, revealing good interactions between layers.
Characterisation of the coatings
This step was performed in Lurederra’s laboratory and saline mist chamber, INL facilities and TSF specific assessment. In this context, it took place the characterisation of the treated samples in terms of performances for each corrosion protection system, regarding adherence, corrosion resistance, hardness, among others. Complementary information has been generated related to microstructure, textures, defects and surface details.
The investigations showed promising results regarding corrosion protection, reaching to more than 4.200 hour of protection in saline mist chamber and successfully comply with corrosion aging test including exposure to salt spray in combination with UV, water condensation and freezing conditions according to ISO 12944-9.
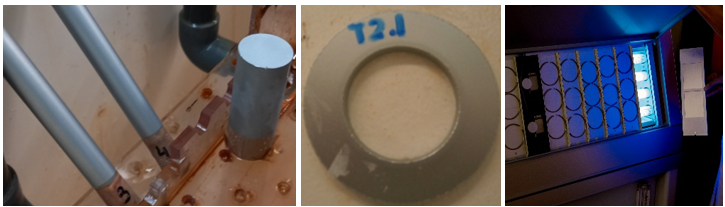
MAREWIND TOWARDS A MORE ECONOMIC AND SUSTAINABLE OFFSHORE WIND SECTOR
MAREWIND project will develop durable materials and recyclable solutions for the offshore wind industry, while extending the service life of the wind facilities and creating new job opportunities.
Nowadays, the wind turbine blade leading-edge erosion affects the annual energy production by 4-20 %. That equates to a loss between €152-760 million a year across the overall European offshore wind sector. Moreover, the maintenance of the materials is very expensive and accounts for around 25% of the offshore wind farms’ cost. In addition to that, at the end of the wind turbines’ service life, the generated waste in need of recycling can increase up to 800,000 tones per year in Europe by 2050.
MAREWIND solutions will pave the way for the next generation offshore wind generators and facilities that aim to solve the technological, economical, business, and societal challenges we are now facing. In addition, it will strengthen the leading role of Europe in the global offshore wind market with current 22,072 MW of installed cumulative capacity, followed by Asian and North America markets.
Meet the consortiumProgress achieved after 18th months
It has been a busy and productive first phase of the project MAREWIND project. Since its launch in December 2020, the MAREWIND team has been working hard on progressing to achieve the ambitious goals of the project. The project addresses the main aspects related to materials durability and maintenance in offshore structures which have the potential to reduce imply failure, misfunctioning, loss of efficiency in energy generation and which have a major repercussion on O&M and CAPEX. MAREWIND aims to develop durable materials and recyclable solutions for the offshore wind industry, while extending the service life of the wind facilities. In addition, the project outcomes will also contribute to meeting the EU climate targets and create new job opportunities within the wind industry.MAREWIND project has achieved its second milestone!
Second milestone of the project has been successfully achieved! During the first year and a half, most of the technical work done by the partners has focused on the fabrication and testing elements individually. Specific formulations have been selected after testing and checking accelerated essays which comply with technical requirements. A great progress has been done thanks to the close collaboration between the partners of MAREWIND consortium. We are looking forward to sharing the outcomes we will achieve in the upcoming years!Next steps
The consortium is preparing its third newsletter, so stay tuned for more details about the progress achieved so far. You can subscribe for the latest MAREWIND news and events, here.MAREWIND is developing innovative structural health monitoring (SHM) systems for blades and foundation structures of offshore wind farms.
Full-field measuring techniques of wind blade working conditions: hardware, measurements and algorithms
In Task 3.1, INEGI is developing a non-destructive testing system which will be a mock-up of the final blade SHM system to be implemented in the following work packages. This system will consist of the use of a drone-supported configuration to perform digital image correlation (DIC) and thermographic analyses to monitor the appearance of surface and subsurface defects on wind turbine blades. At this stage, INEGI has already worked on the preliminary studies to define and design the laboratory testing setups to be carried out and on the selection of all the necessary equipment (Figure 1). Subsequently, INEGI also started to work on the synchronized trigger and control solution related to the DIC analyses.
Finally, with regard to image acquisition and processing tasks, INEGI has already performed some test setups for DIC and infrared (IR) analysis. For the future, INEGI will focus on the implementation of all proposed configurations for the validation of the proposed technology and will also work on the development of the data analysis software necessary for the implementation of the real-case scenario.
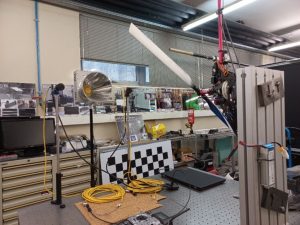
Implementation and assessment of FBGs/DFOs technologies for composite
Likewise, in Task 3.2, INEGI is responsible for the development and implementation of embedded fibre optical (FO) sensors for representative laboratory composite components. As of this date, INEGI has already worked on defining the location of the sensors for all the variables to be assessed, defining the equipment used for each parameter evaluated and started its procurement process.
In addition to this, INEGI has already run three test setups with representative parts instrumented with both conventional strain gauges and Fibre Bragg grating (FBG) sensors (2), which allowed to validate the proposed sensor placement, access the sensor bonding process and start developing the data acquisition and processing software. For the future, INEGI plans to complete the execution of all the proposed configurations and to work on the development of the data acquisition and processing software.
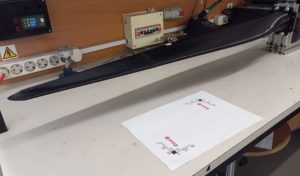
In the same Task 3.2, CETMA is responsible for the development and implementation of the innovative SHM system, based on FO, that will be used for monitoring the foundation structures of offshore wind farms. Prototypes of the foundation structures to be built with the new mixtures were defined, based on a new design, in collaboration with the other partners involved; the SHM monitoring system was defined in terms of number and positions of points to be monitored, frequency of acquisition, parameters to be monitored and costs of equipment and sensors. All these parameters brought to the definition of SHM system based on distributed FO sensors to be apply on composite rebars in the concrete structures. In the next months, CETMA will carry out lab trials on the SHM system to demonstrate the suitability of the designed solution to the application.
Water simulations around gravity-based structures
In Task 3.3, INEGI will develop models to recreate the operational conditions of a Ground Based Structure (GBS). These models will consider three scenarios: transport to the installation site, installation and operation. With the information provided by these models and using machine learning algorithms it will be possible to obtain information about the GBS in real environment aiming the decision of the need of maintenance.
At this stage, the Computational Fluid Dynamics (CFD) numerical simulations that model the water flow around the GBS are running, with some results already obtained. This data follows to Fluid-Structure Interaction (FSI) models to quantify the efforts on the GBS (Figure 3). The machine learning models were already developed and are ready to be trained with the data produced by CFD and FSI models.
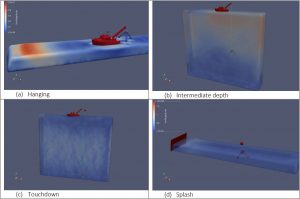
Structural analyses on composite blades
In the period M4-M12, RINA has continued the development of a mathematical model of the composite blade materials by developing the high-resolution finite element model for composite blades (Figure 4). In addition, RINA has developed a MS Excel tool able to perform a preliminary micro- and macro-mechanical analysis on flat composite structures made of unidirectional fabrics. Both the tool and finite element model have been preliminarily validated with a reference composite structure (experimental data available and provided by the partner EIRE Composites).
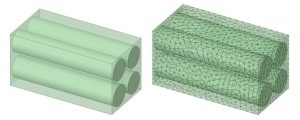
The next steps will consist in performing a more accurate calibration and validation of the high-resolution finite element model of composite and tool, also testing the in-use materials selected for the development of the prototype. The results will be the basis for conducting the activities referred to the simulation of the blade prototype (or part of it) to predict the fatigue life of the wind turbines.
Modelling of corrosion in atmosphere-exposed metallic structures
From month 6 to month 12, IDENER continued the formulation of a corrosion mathematical model that considers the protection of the metallic surface with an anticorrosion coating layer. The model simulates the dynamics of the interface between the coating and electrolyte. The first version of the model has been implemented in a computational environment, in one and two dimensions, and tested with variable input to detect anomalies in the generated results or convergence issues. In the following steps, the new corrosion experimental results generated by the partners Lurederra, TECNAN and INL will be analyzed and used for the calibration of the model.
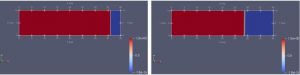
During WP2 different activities have been handle aiming at the fabrication and testing elements individually.
In Task 2.1 and Task 2.2, Lurederra, strongly supported for the coating manufacturer TECNAN, focused on the formulation, application and optimization at lab-scale coating for anticorrosion on metallic materials and antifouling coatings for metallic and plastic materials. In addition, TWI leader of Task 2.3 led the anti-erosion superhydrophobic paints for leading edge protection.
Anticorrosion coatings for metallic elements
The coating would consist in three layers with different chemical composition and therefore different complementary corrosion protections.. The development of the formulations for the different layers shows a very good trend, implying suitable performances for each case, regarding adherence, corrosion resistance, hardness, etc., highlighting the promising results with low temperature matrices, and the process with the self-healing fibers with the main focus on their integration (Figure 1).
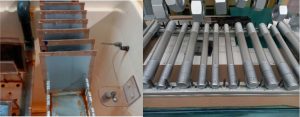
The development of the self-healing nanofibers is also showing promising results according to its specific characterization for its functionality. Moreover, the recent progress for the dispersion of those active fibers is enabling first application tests by spraying, so the multi-layer approach envisaged in the project is getting closer.
Concerning the coating application system, two strategies were mainly designed for this purpose: application via spray gun and application via dip coating. Spraying is the main alternative, since it provides a good surface finish, being applicable for different morphologies and sizes.
Antifouling coatings development, production, application and testing
A fouling-preventing coating for different materials of offshore structures that are submerged are being developed at laboratory scale.
Various highly repellent (hydrophobic and oleophobic) coatings are in development showing also a good adherence and low number of defects. Despite some adjustments are in progress, in a preliminary way, the formulations seem suitable for preventing biofouling formation.
The initial tests to multiple substrates with different chemical nature have been successful. This fact is supported by a considerable number of physicochemical characterizations on different substrates (metal and polymeric). Apart from the experimental work in formulation and characterization, the work related to the collection of reference information has been helpful, highlighting specially the selection of benchmark products from the market.
The application of the anti-fouling coatings is via spray gun (Figure 2), as the most suitable method for this objective, due to its versatility for the different target applications.

Anti-erosion superhydrophobic PU coating for blades: development, production, application and testing
The selection of the wind turbine blade coating matrices were based on the commercially available systems. A survey of the commercial leading edge protection coatings has been carried out and the candidate coating systems were shortlisted. In order to achieve the desired repellence (superhydrophobicity) and erosion resistance, TWI have incorporated functional additives into the selected coating matrices.
The selected additives were based on materials available within the project and which have previously been demonstrated to be platforms for superhydrophobic surfaces. These additives are inorganic metal oxides that are capable of surface functionalization to enable their native hydrophilic surfaces to be transformed into exhibiting hydrophobic behavior. The key additives that are explored are:
- Stöber derived TWI silica
- Metal oxides (TECNAN’s silica manufactured using pyrogenic methods and commercially available pyrogenic silica Aerosil 200)
The functionalization of particles – TWI, TECNAN and commercial pyrogenic silica – has demonstrated to significantly change the surface chemistry and thus, uplift the repellence. Also, viscosity versus loading studies (Figure 3 and 4) illustrate the impact of shear rate on viscosity and the difference in behavior between pyrogenic and TWI Stöber silica, suggesting that only TWI silica can be loaded high without a significant change of epoxy or PU physical behavior. The addition, all functionalized silicas added into polysilazane model system improved the repellence characteristics of the whole coating system and thus, it is believed that this will lead to enhanced rain erosion resistance. Besides that, the addition of silica doesn’t affect the coating surface roughness, which means that aerodynamic performance of blades won’t be impacted.
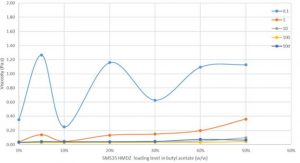
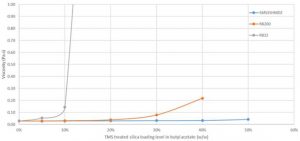
Synthesis of new concrete materials, testing of increased durability and corrosion resistance
In month 4 within Task 2.4, ACCIONA along CETMA, INEGI and EDF started developing and testing at laboratory level innovative concrete mixtures with the aim of increasing durability and corrosion resistance. The main effort was focused on the design of:
-
High and ultrahigh concrete material: During this months, the main effort regarding High and Ultrahigh concrete design, were focused on the selection of materials which best fits the offshore application requirements. From the data obtained to date, it could be state that the best materials are a combination of CEM I 52.5 mixed with active additions from waste, a latest generation superplasticizer additive and silica aggregates. This lead to mortars and concretes with higher mechanical properties and workability helping on samples manufacturing process. HPRFRC dosage has been optimized and meets design requirements. It has low potential for cracking according to the ASTM C1581/C1581M Standard. HPFRC optimized dosage has very high resistance against water and chloride penetration (Figure 5).
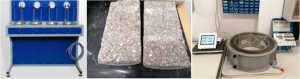
-
Alkali Activated concretes that fulfil offshore infrastructure requirements. CETMA, which is responsible for the development of cementless concrete, divided the activity into three main phases:
- Binder design (Figure 6)
- Mortar design and development
- Concrete development and AAM (alkali activated materials) testing
AAM high-density concrete is under development. Although some adjustments are in progress, the binder and mortar formulations have provided good results for the purposes of the project.
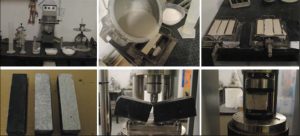
- Chlorides ingress characterization for aging concrete in marine environment: EDF is responsible for providing data from ageing concrete samples fabricated directly at the Blyth Wind Farm construction site. 4 months and 1-year aged specimens under permanent immersion have been considered to evaluate the chloride ions ingress. Each specimen of Ф16 cm x10 cm dimensions, is sealed with epoxy resin to allow the penetration of chlorides from a single face, as shown in the figure below. Each sub-specimen has been subjected to the chemical analysis according to the EN14629 standard. Powders corresponding to 10 different depths were manufactured and used to determine the chlorides content. With 9 and 10 tested specimens after respectively 4-months and 1-year of seawater exposure, a comprehensive database of chloride content distribution is available. Some basic processing including the determination of the chloride apparent diffusivity and the prediction of chlorides content evolution over time were performed, in this context. This database will allow the evaluation of new materials (Figure 7).
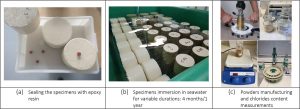
Reinforced composites production and testing
In Task 2.5, the following three strategies were planned for new composite laminate production, which involves close collaboration between task leader ÉireComposites (EIRE), TWI and CETMA.
- Use of nano-SiO2
- Use of RCF (Recycled Carbon Fibers)
- Use of /TPR (Thermoplastic Reactive Resin)/Recyclable Epoxy resins
EIRE supplied powder and liquid epoxy resins to TWI and CETMA, for new resin formula and composite reinforcement development. In addition, EIRE defined a preliminary and final material text matrix that will be used to characterize the mechanical and physical properties of the composite laminates produced.
On the other hand, CETMA has defined a preliminary numerical model for the simulation of the resin infusion process, and it has also set up the RCF/Epoxy infusion process with mechanical characterizations in order to adjust the final properties of the new composite formulations.
TWI have characterized and functionalized both, pyrogenic silica and Stöber silica, including wetting behavior and loading effects upon the incorporation to DBEBA epoxy model system. The functionalization has a significant impact on the surface chemistry of those silicas, making them superhydrophobic. Addition of functionalized silicas into DGBE remains a significant challenge, as it raises the viscosity (Figure 8). Nevertheless, this will be mitigated by the development of appropriate silicas incorporation/mixing techniques.
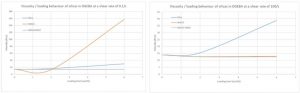
Preliminary testing of the recycling process and prediction of properties
In Task 2.6 CETMA has carried out rheological and thermal analysis of selected formulations of thermoplastic reactive resins and recyclable thermoset resins. In scale-up activities of the recycling process the most promising recyclable resin and related recycling method will be selected in terms of both initial component performance and industrial effectiveness of the recycling procedure.
Additionally, CETMA also generated a multi-scale numerical model of the recycled material based on RCF. A Representative Volume Elements (RVE) of the recycled material has been generated (Figure 9) and the numerical analyses to calculate the mechanical properties of the composite laminate have been carried out (Figure 10). The good agreement between the numerical and the experimental test results demonstrated the high reliability of the numerical model.
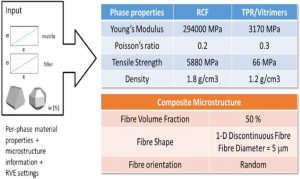
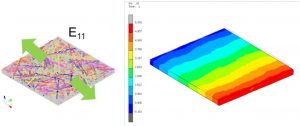