New concrete materials to increase durability and corrosion resistance
03 August 2022
During the first 18 months of the project, the main effort has been focused on the design of high, ultrahigh performance concrete and Alkali Activated concretes that fulfil offshore infrastructures requirements. In addition, EDF has performed tests to evaluate the durability of concrete under exposure to the real environment through aging tests. It also provided support on floating offshore concrete structures, including contribution on modeling of the structures that will be used to design the prototypes to be tested.
High and ultra-high Concrete material
The reference material (Class C60 concrete) was defined from a previous experience on offshore concrete design. The work was focused on new advanced concrete materials design. After preliminary laboratory trials for the optimal raw material selection, the proper combinations were selected for high and ultra-high concrete mixtures design.
To fulfil the high performance concrete requirement, 9 dosages were casted and tested. Thedesign and optimization of the ultra-high concrete was more challenging compared to HPC, due to the occluded air that remained in the samples in the casting process.
According to the standard recommendations, HPC has low potential for cracking under restrained conditions; UHPC with PVA fibres has moderate-low potential, UHPC without SAP (super absorbent polymer) additive has moderate-high potential, UHPC with SAP additive and conventional concrete have high potential for cracking under restrained conditions. Thanks to the higher content of SCM in UHPC samples, the heat of hydration of these mixes in lower than for HPC. Therefore, showing very promising results for the advanced concrete materials developed within this task.

Alkali Activated concrete
CETMA has focused on the development of alkaline activated conglomerates (AAC), considering only alkaline activators, glass powders and blast furnace slag were used as binder.
Since alkaline activated materials have a very viscous behaviour and generally have very fast setting times, they are hard materials to mix. To avoid excessive consumption of materials and safeguard equipment, the experimental program was divided into three different phases:
-
First phase: the behaviour in the fresh and hardened state of the binder composed of glass powders, blast furnace slags and activators such as water, sodium silicate and sodium hydroxide were characterized.
-
Second phase: previously optimized binder was mixed with four different types of sand for the realization and characterization of alkali activated mortars.
-
Third phase: based on previously characterized binder and mortars, AAC mix design containing three different types of aggregates was carried out.
To increase AAC mix sustainability, optimized binder-recycled aggregates compatibility was studied. Furthermore, very fine natural magnetite was used to increase the density and try to reduce the cracking phenomena caused by the heat of hydration. After choosing the best performing mix design to achieve project specifications in terms of compressive strength, consistency and workability, a final proportion optimization and repeatability study was performed.
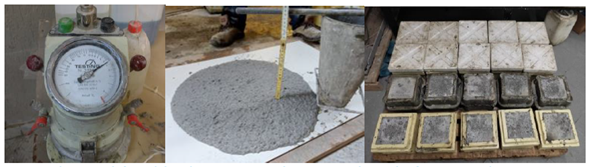
MAREWIND concretes durability characterization
For durability characterization of new concrete materials developed in MAREWIND project, several tests were carried out. Test results show that advanced concretes, as it was expected, are able to achieve better durability performance than standard C60 offshore concrete . Both advanced concretes showed in general, the same durability results, only in corrosion rate and probability UHPC presents a slight risk. Despite these slight differences, UHPC will be used on the prototype manufacturing due to its SCC behavior, that allows slender structures more suitable to keep floating structure’s buoyancy.
AAC presented similar behavior as C60 concrete in chloride penetration resistance, it showed better performance at early-ages to water penetration, whereas it seemed to be likely to develop corrosion risk during it service life. A deeper analysis will be carried out when all the ages results will be available, to check if this tendency keeps in time or not.
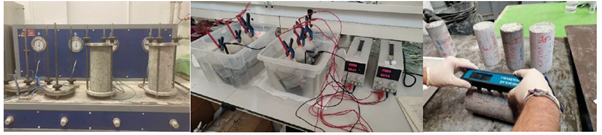
Durability of concrete samples exposed to a real environment
EDF performed the reference characterization of the durability properties of an ordinary offshore concrete mixture in their offshore facilities.
Chloride ingress in permanent immersion and tidal zone exposure is characterized in ϕ16×32 cm cylindrical specimens. Each sample has been divided into 3 sub-specimens of ϕ16×10 cm. The obtained sub-specimens have been subjected to chloride ingress. A first group was immersed completely in seawater, whereas, a second group was subjected to wetting/drying cycles with 6 hours period using a hydraulic pump.
As result, a comprehensive database of chloride content distribution was set up. Some basic processing including the determination of the chloride apparent diffusivity and the prediction of chlorides content evolution over time were performed.