Fabrication and testing elements
25 August 2021
The second part of the MAREWIND work plan WP2 Fabrication and testing elements individually has started in March 2021 and is led by Lurederra. Within the scope of work is to formulate and optimize at a lab-scale different material. The consortium will improve corrosion protection, fouling prevention, blade’s coating protection, blade’s composites optimisation, recycling and concrete enhancement. The partners involved in this WP will also oversee the synthesis and selection of new concrete materials and testing/aging at lab scale. The task is still on going and will be active until M18, May 2022.
Development of improved materials
MAREWIND project is focused on cost reduction related to material durability and maintenance in offshore structures. Therefore, the development of improved materials is a strong activity which has started on a laboratory scale. On this regard, various action points have been already taken in the offshore wind turbines to improve their performance. Concretely:
- Anticorrosion coatings
- Antifouling coatings
- Antierosion coatings
- New concrete materials
- New reinforced composites
At this stage of the project, each development point has progressed and showing relevant results already. In the case of anticorrosion for metallic materials, the key is to prevent degradation. This is achieved by generating an extremely high protective system to avoid the contact of moisture with the metallic alloys used in different parts of the windmills. For instance, one of the project focuses are fastening elements, but also additional parts like tower flanges and blade bearings, which are typically subjected to atmospheric corrosion.
The project strategy to tackle this issue, is based on advanced chemical formulations for a multi-layer treatment including nanotechnology. On this regard, LUREDERRA has already started working on different formulations for anticorrosion coatings. This activity will be carried out in collaboration with INL and includes the preparation and integration of self-healing ingredients.
The research team has also started the laboratory testing with coatings on reference square coupons and real fastening elements. At laboratory scale, a complete characterisation is envisaged. That includes not only detailed surface analysis with SEM or AFM, but also testing of the anticorrosion performance in saline mist chamber, simulating a realistic environmental menace.
It is worth highlighting, the current results obtained regarding the resistance of several coated pieces in hours of saline mist chamber (ISO 9227), which are really promising; since relevant requirements indicate 1440 h, and already more than 2000 h have been successfully completed without damage. Therefore, good prospects are envisaged for most demanding requirements of the offshore sector, which indicate more than 4200h.

Apart from the development of anticorrosion coatings for metal surfaces, the partner KOSHKIL is also further progressing with their study about different areas and materials that are subjected to corrosion.
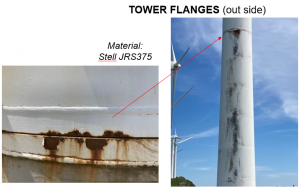
Meanwhile, the researchers are also fully occupied with antifouling coatings formulation. Main elements susceptible to fouling are foundations, mooring lines as well as inter-array cables. However, the main issue in this case is the adherence of biological content to all the mentioned surfaces, modifying the morphology, performance and weight of the structure, and some time also progressively degrading them chemically.
The project solution is based of avoiding this foulant phenomenon without using biocides. Therefore, an outstanding anti-adherent effect is required, and also highly versatile, to be used in submerged metals and polymers. Various formulations based on TECNAN background have been prepared and different substrates were applied with relevant result.
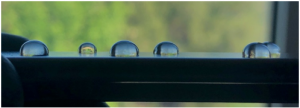
The MAREWIND team is also developing antierosion superhydrophobic coatings for blades. More in details, wind turbine blades are aerofoils similar to aircraft wings but fixed in place and positioned vertically. The similarity extends to the fact that anything disruption to the aerodynamic performance of the blade affects its efficacy and ultimately reduces the power output of the turbine. The two main causes of loss of aerodynamic efficiency are the accretion of surface contamination (ice, dirt, insect debris) and erosion changing the profile of the blade.
In this context, MAREWIND project proposes reduction and prevention of surface contamination through the use of highly repellent surfaces. These are expected to improve aerodynamic efficiency, increase safety, reduce maintenance costs and minimise the use of chemicals, which foul ground water. Whilst each of these drivers is significant in its own right, conventional coatings and approaches do not deliver the performance needed due to lack of long-term erosion resistance.
In addition, there are existing supply chain infrastructures, application procedures, materials selection, specification protocols and procurement routines in place for the coatings that are used today. New coatings need to fit into the existing practices but they must also deliver enhanced benefit. This challenge is significant, but the drivers provide the motive force. Precisely, one of the objectives of MAREWIND project in this WP is to bridge the gap between high repellence and erosion resistance.
Moreover, within the project TWI is developing new functional building blocks that can be integrated into current class-leading erosion resistant coatings. Thus, it will provide the required performance uplift. The core of this emerging technology is sol-gel and the common feature of the building blocks are metal oxides particles. This approach allows the design and fabrication of new functional materials, and the opportunity to provide capabilities that have not previously been possible.
Surface functionalization allows these oxides particles to be made compatible with organic resins. Thus, enabling high loading levels without segregation, gelation or the need for diluents, which accounts for increase of durability, and thereby erosion resistance. Moreover, the ability of grafting specific chemistries on these particles offers the opportunity to tailor and tune the attributes of the whole coating system, e.g., providing superhydrophobic properties.
A key measure of repellence to validate this approach is water contact angle, going from <10° to ~150° (Figure 5). Thus, the next phase of the project is to prepare coatings incorporating these functional additives and to test their performance characteristics.
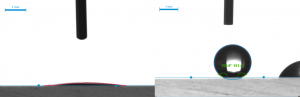
As of March 2021, the synthesis and selection of new concrete materials (Activated Alcali Materials-AAMs and Ultra High-Performance Fibre Reinforce Concrete-UHPFRC) and testing/aging at lab-scale has also started. Reference material to compare the MAREWIND solution is C60 concrete used for offshore structures.
The research team carried out a compressive strength test and evaluated the type of cement. A compatibility of two additives with the selected cement was analysed as well. Optimum quantity of additive is calculated for each tested recipe. In the next tests the consortium will design UHPFRC and HPFRC (High Performance Fibre Reinforce Concrete) using cement and selected additive.
On the other hand, cement free concrete will be used to perform one of the three foundations of the GBS structure. For this, binder development is on-going in order to develop afterwards mortar containing the optimised binder and develop and testing the AAMs concrete.
Reinforced composite production and testing started also in M4 (March 2021) of the project. Up to now, preliminary test matrix has begun too. In the next months, infusion resin and specific functionalised nanosilica will be provided. Final test matrix to generate material dataset is expected in M13 (December 2021).
Last task from WP2 is related with recycling processes and the corresponding preliminary testing has started. The consortium has already begun with the design of the strategy for recyclable thermoset resin. In addition, the partners are actively working on the respective tasks for development of a multi-scale numerical model. In the following months, the partners will carry out sensitivity numerical analysis to evaluate the effects of the intrinsic variability of the recycled composite on the final properties.